Nachrüstung von Arbeitsbereichsüberwachungen für Schiffsverladearme –
im großen Stil und mit besonderen Vorgaben
Was tun, wenn Schiffsverladearme in die Jahre gekommen sind und nicht mehr aktuellen Sicherheitsanforderungen entsprechen? Vor diesem Problem stand einer unserer Kunden. Um behördliche Auflagen erfüllen zu können, musste er an einem Standort gleich 18 Verladearme mit einer automatisierten Arbeitsbereichsüberwachung nachrüsten. Bis dato verfügten die Verladearme zwar über Not-Trenn-Sicherungen. Diese waren aber nicht an eine permanente, durch Induktoren erfasste Kontrolle des Schwenkbereichs gekoppelt. Sprich: Es musste immer ein Mitarbeiter abgestellt werden, der dann auf die Einhaltung des Schwenkbereichs achtete und die Not-Trennung gegebenenfalls manuell auslöste. Das erforderte nicht nur höheren Personalaufwand, es barg auch ein gewisses Risiko für Mensch, Material und Umwelt. Diese Situation sollte durch eine neu konzipierte automatische Arbeitsbereichsüberwachung geändert werden. Natürlich mit möglichst geringen Ausfallzeiten und durch optimal wirtschaftliche Lösungen.
Erstellung individueller Arbeitsbereichspläne
Am Anfang jeder automatisierten Arbeitsbereichsüberwachung steht die Definition der jeweiligen Arbeits-, Warn- und Trennbereiche. Hierfür haben wir für jeden Schiffsverladearm vorhandene Angaben herangezogen, geprüft und dann gemeinsam mit dem Kunden, unter Berücksichtigung des jeweiligen Standorts und der dortigen Infrastruktur, einen individuellen Arbeitsbereichsplan erstellt. Darin ist dann neben dem sicheren Arbeitsbereich auch genau definiert, ab welcher vertikalen und horizontalen Ausschwenkung eine Warnung ausgegeben bzw. die Not-Trennung initiiert wird. Beide Zustände werden durch unterschiedliche akustische und optische Signale angezeigt, wobei das zweistufige System korrelierend aufgebaut ist. Bedeutet: Bereits im Warnbereich wird der Materialfluss automatisch gedrosselt, um eine eventuell zu erfolgende Not-Trennung so sicher und anlagenschonend wie möglich ablaufen zu lassen. Zur automatischen Trennung, deren Auslösung an der Anlage akustisch und optisch angezeigt wird, kommt es erst, wenn der Verladearm in den Trennbereich gelangt.
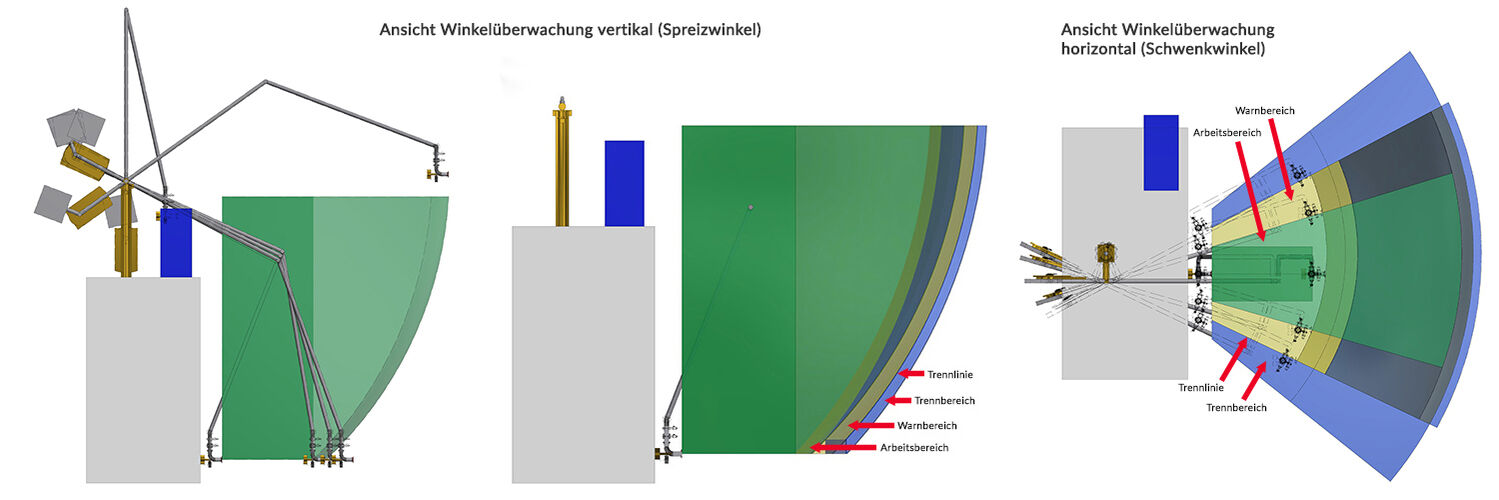
Fokus auf Umweltschutz, Arbeitssicherheit und Anlagenverfügbarkeit
Ziel einer Arbeitsbereichsüberwachung mit induktionsgesteuertem Not-Trenn-System ist grundsätzlich, die Schiffsverladung maximal sicher zu machen. Schließlich besteht bei diesem besonderen Verladungsszenario immer die Gefahr eines abgleitenden Schiffs. Mögliche Folgen sind, dass die Verladearme Schaden nehmen bzw. schlimmstenfalls die Verbindung zum Schiff abreißt und Umschlagmaterial unkontrolliert ins Wasser strömt. Vor diesem Worst-Case-Szenario schützt bereits der Einsatz normaler Not-Trenn-Kupplungen an den Anschlussgruppen von Schiffsverladearmen. Mit einem System, wie wir es hier in diesem Beispielprojekt umgesetzt haben, lässt sich die Sicherheit aber nochmal erhöhen. Durch die unterschiedlichen vom System ausgegebenen Warnungen gibt es noch genug Gelegenheit zum Reagieren und die Wahrscheinlichkeit, eine Gefährdung nach Trennung durch automatisierte Prozesse zu verhindern. Das gilt umso mehr, als es sich bei der von uns realisierten Arbeitsbereichsüberwachung um ein sehr zuverlässiges System handelt. Die Warn- und Trennbereiche werden durch induktive, NAMUR-fähige Näherungsschalter erfasst, die sich selbst überwachen.
Zusätzliche Sicherheit durch manuelle Freischaltung des Systems
Ein zusätzliches Feature des von uns realisierten Systems besteht darin, dass die Not-Trenn-Funktion vom Bediener auf aktiv oder inaktiv gestellt wird. Hierfür gibt es eine separate, an der Anschlussgruppe des Schiffsverladearms befindliche, Bedieneinheit mit Drehregler und induktiver Schaltstellenüberwachung. Durch das händische Aktivschalten der Not-Trenn-Sicherung kann zuverlässig verhindert werden, dass diese versehentlich ausgelöst wird, wenn gar kein Schiff an dem Verladearm angeflanscht ist oder sich gerade Personen im Gefahrenbereich der Sicherheitstrenneinrichtung befinden. Der Bediener schließt also immer zuerst den Verladearm an und schaltet das System erst danach und beim Verlassen der Anschlussstelle auf „scharf“. Ein weiteres Extra direkt an den Anschlussgruppen der Verladearme besteht darin, dass wir in Sonderausführung für alle 18 Schiffsverladearme Stützfüße angefertigt und installiert haben.
Wie immer galt: Ausfallzeiten vermeiden
Neben dem Umfang des Projekts mit der Nachrüstung von insgesamt 18 Schiffsverladearmen gab es auch zusätzliche organisatorische Herausforderungen. So war kundenseitig für die Arbeiten an jedem Verladearm ein Zeitfenster von täglich max. 12 Stunden vorgegeben, um keine Einbußen bei den Verladekapazitäten zu haben. Danach mussten die Verladearme wieder einsatzbereit zur Verfügung stehen. Unnötig zu erwähnen, dass dafür jede Bauteillieferung und jeder Handgriff auf den Punkt sitzen musste. Erschwerend hinzu kam, dass im Prinzip kein Schiffsverladearm wie der andere war und jeder ein eigenes Nachrüstungsprojekt für sich darstellte. Wir hatten es mit Schiffsverladearmen von unterschiedlichen Herstellern zu tun, wobei von jedem Hersteller auch verschiedene Modellgenerationen im Einsatz waren. Von Standardlösungen ist alles das weit entfernt. Aber das gilt für Nachrüstungen bei Schiffsverladearmen generell. Immer geht es darum, die für die jeweiligen Anforderungen maßgeschneiderten Lösungen zu entwickeln. Bei allen Modernisierungsmaßnahmen von Schiffsverladearmen identisch ist hingegen, dass sie zahlreiche Vorteile mit sich bringen und eigentlich immer die bessere Alternative im Vergleich zur kompletten Neuanschaffung sind. Lesen Sie hierzu auch die Vorteile in unserem Bericht Warum sich die Modernisierung von Schiffsverladearmen lohnt.
Komplett autarkes System oder Einbindung in PLT – alles ist möglich
Automatisierte Systeme zur Überwachung lassen sich wahlweise komplett geschlossen oder eingebunden in die Prozessleitstelle anlegen. In unserem Beispielprojekt für die Arbeitsbereichsüberwachung von Schiffverladearmen funktioniert das System nicht autark, sondern wurde in die Prozessleittechnik des Kunden eingebunden.
Alternativ können auch autarke Systeme eingesetzt werden, die Meldungen oder einzelnen Zustände an die Prozessleitstelle herausgeben, damit zum Beispiel von hier der Materialfluss bei Bedarf gedrosselt wird und dies nicht automatisch geschieht. Hier sind den Kundenwünschen keine Grenzen gesetzt.
Sprechen Sie uns einfach an. Wir entwickeln für Sie die Lösung nach Maß.